Saved $1M in construction cost
40% Energy Savings and LEED Platinum
Saved 240 Hours from Design Revisions
01// Project Overview
At 117,00 sq. ft., the Campus Life Center on the Emory University campus caters to the growing space demands, allows flexibility and efficient dining services, technology and infrastructure upgrades, and more room for student organizations and gathering space. With the University’s commitment to sustainability, the Campus Life Center has high performance targets
02// Climate Analysis
03// Energy Analysis
04// Daylight and Glare Analysis
05// Facade Studies
06// Water Use Analysis
07// Cost Vs Energy Optimization
Related Posts
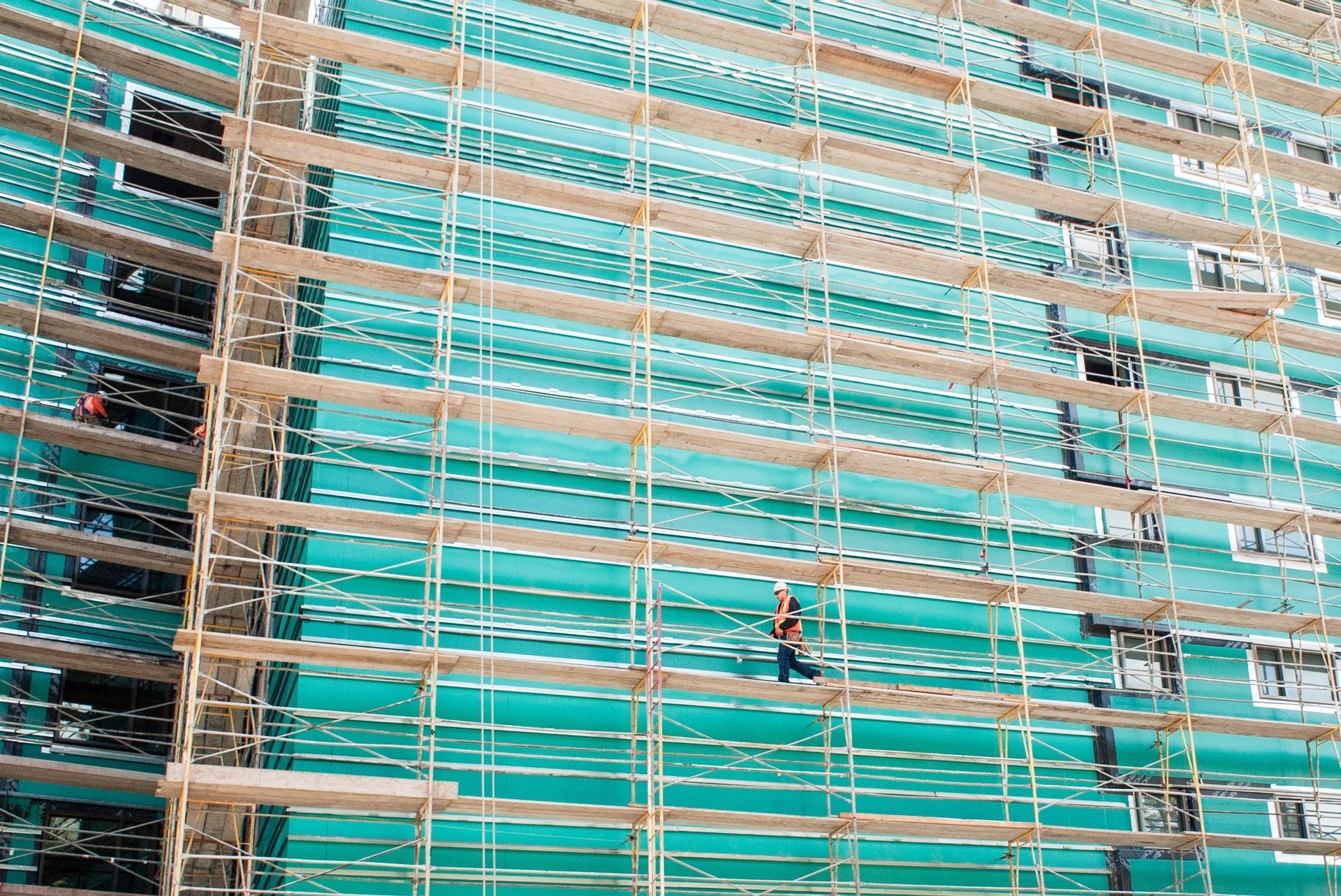
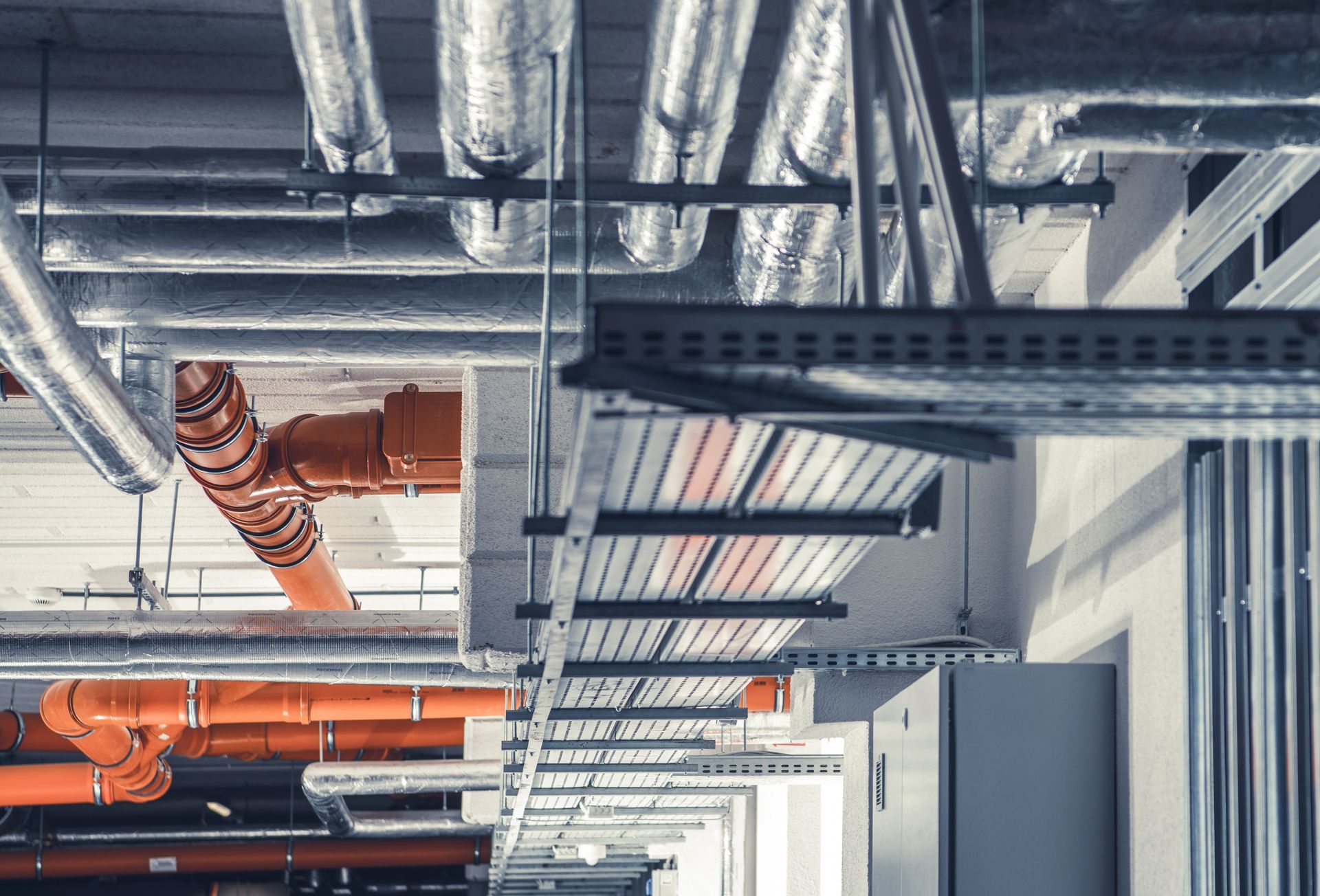
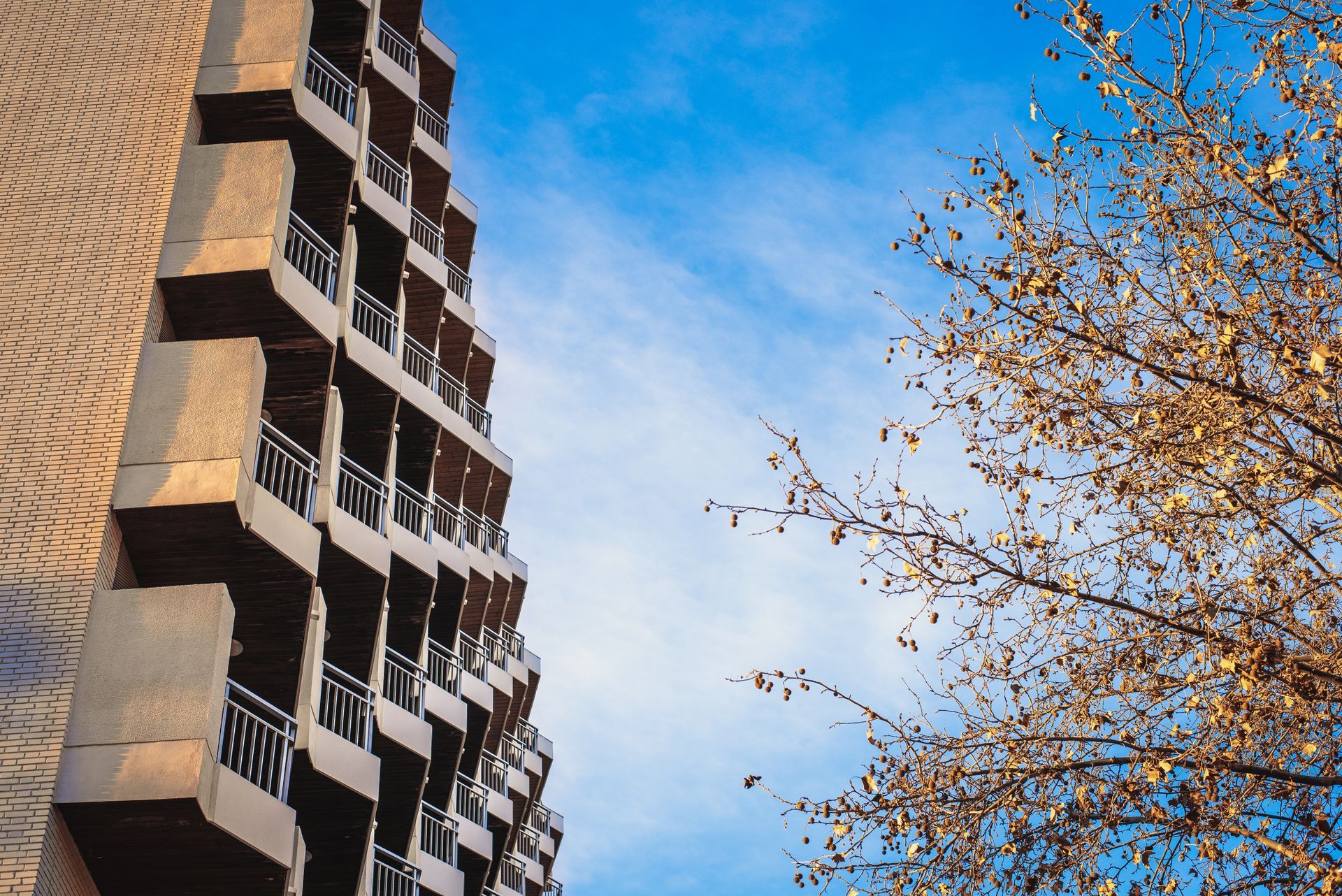